Significance
Fresh Press is the only research lab at a university in North America focused on the testing and creation of papers and building materials that are viable for commercial use from agricultural residue fiber sourced from an on-campus sustainable farm (Fig. 1). The research and community engagement ecology of the lab is akin to an amoeba (Fig. 2), one that is active and changes with each new scholar or student who joins.
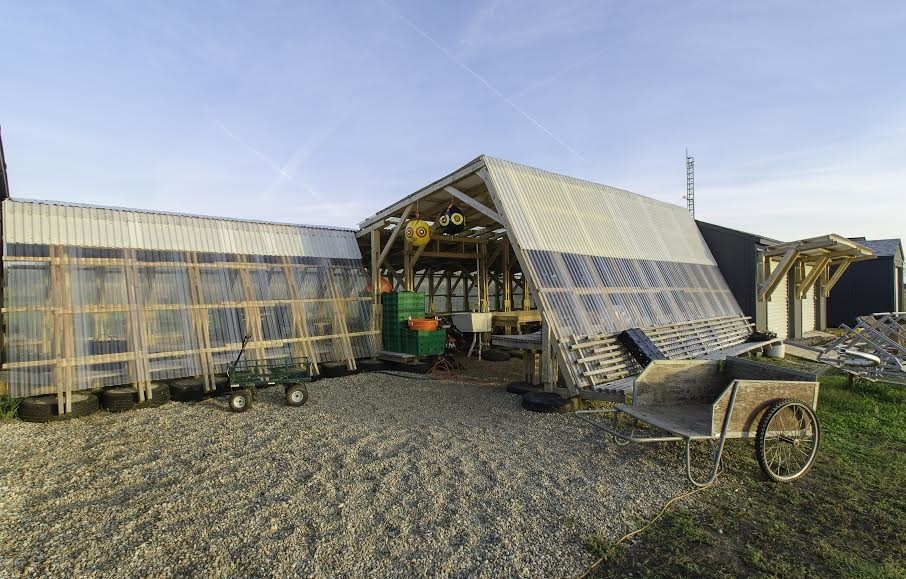
Background
When the lab began after our first round of grants in 2012, Fresh Press consisted of two designers (Eric Benson & Steve Kostell) and organic farmer Zack Grant. Since then, our lab has grown to conduct and publish research with architects, mechanical engineers, artists, chemists, entomologists, and book conservationists. Fresh Press has received $242,383 in total grant funding over ten years from the University of Illinois Student Sustainability Committee and the University of Illinois Campus Research Board. Our mission has always been to change the paper supply chain from forest to farm. We aim to make and promote agri-fiber paper and paper products as environmentally friendly substitutes for tree fiber. To complete our mission, we need a team of collaborators and funding.
This ecology of collaborators has worked in the following fashion. The Sustainable Student Farm (SSF) provides agricultural fibers to be used in scholarship by artists, designers, librarians, and architects for two- and three-dimensional materials (paper and construction materials predominantly). These materials are tested and analyzed by both engineers and chemists to collect data on their individual properties. One important analysis in material science is the stress-strain test that shows the amount of load or stress that a paper can handle before it stretches and breaks (Fig. 3). For Fresh Press, we are interested in the tensile stress and strain to gauge its elasticity. The strength and elasticity a paper demonstrates in the testing helps us know how the paper will function in different roles. For example, this stress-strain data for corn mixed with recycled cotton shows those fibers are stronger than corn fibers alone and could be used for many projects. We have used corn paper in some consistent themes: art on paper (Fig. 4), paper as art (Fig. 5), “corncrete” building blocks (Fig. 6), and case paper for book conservation and binding (Fig. 7).
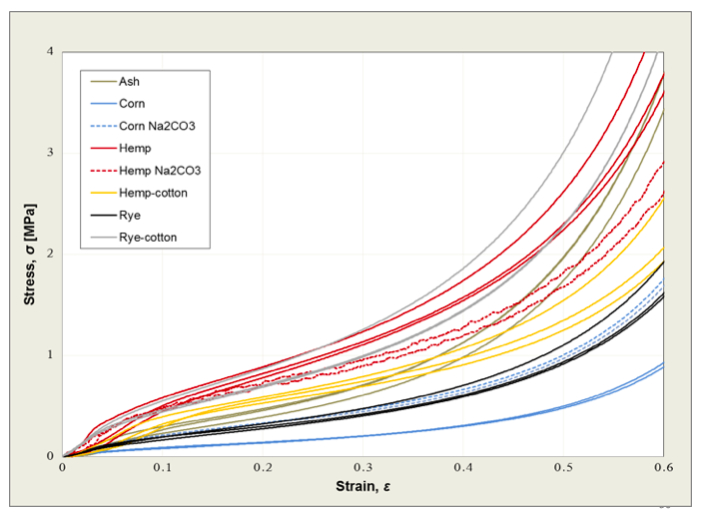
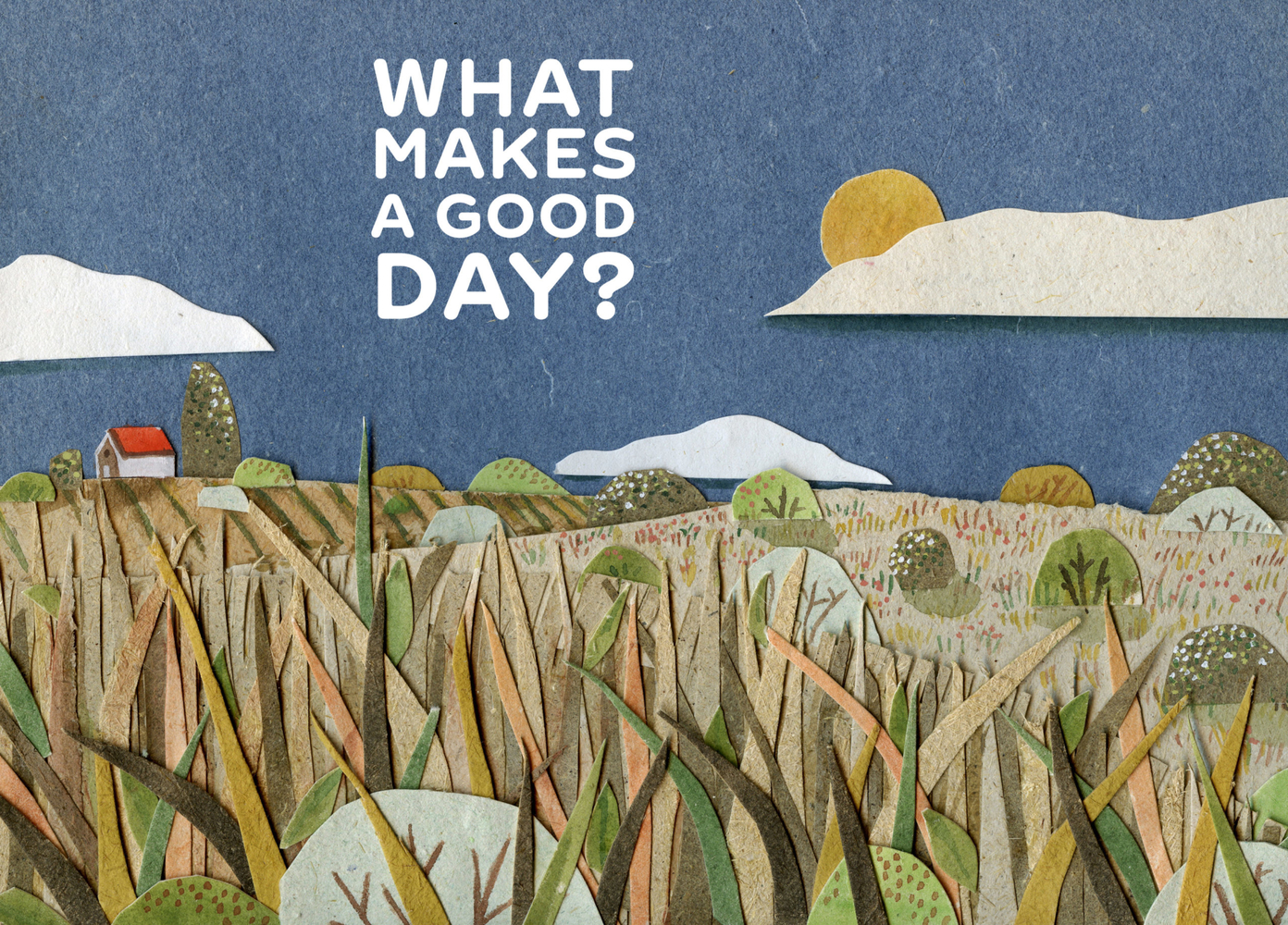
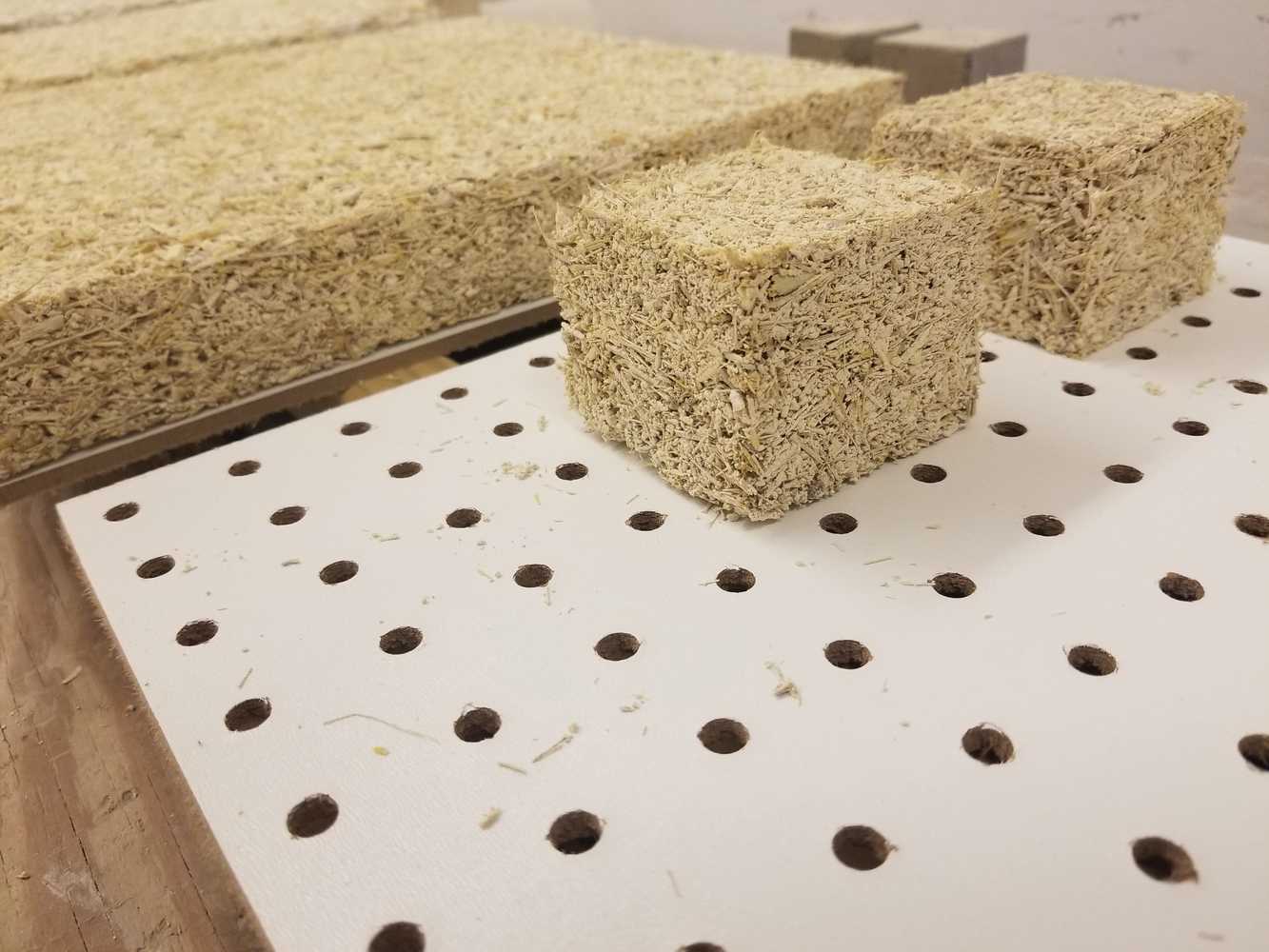
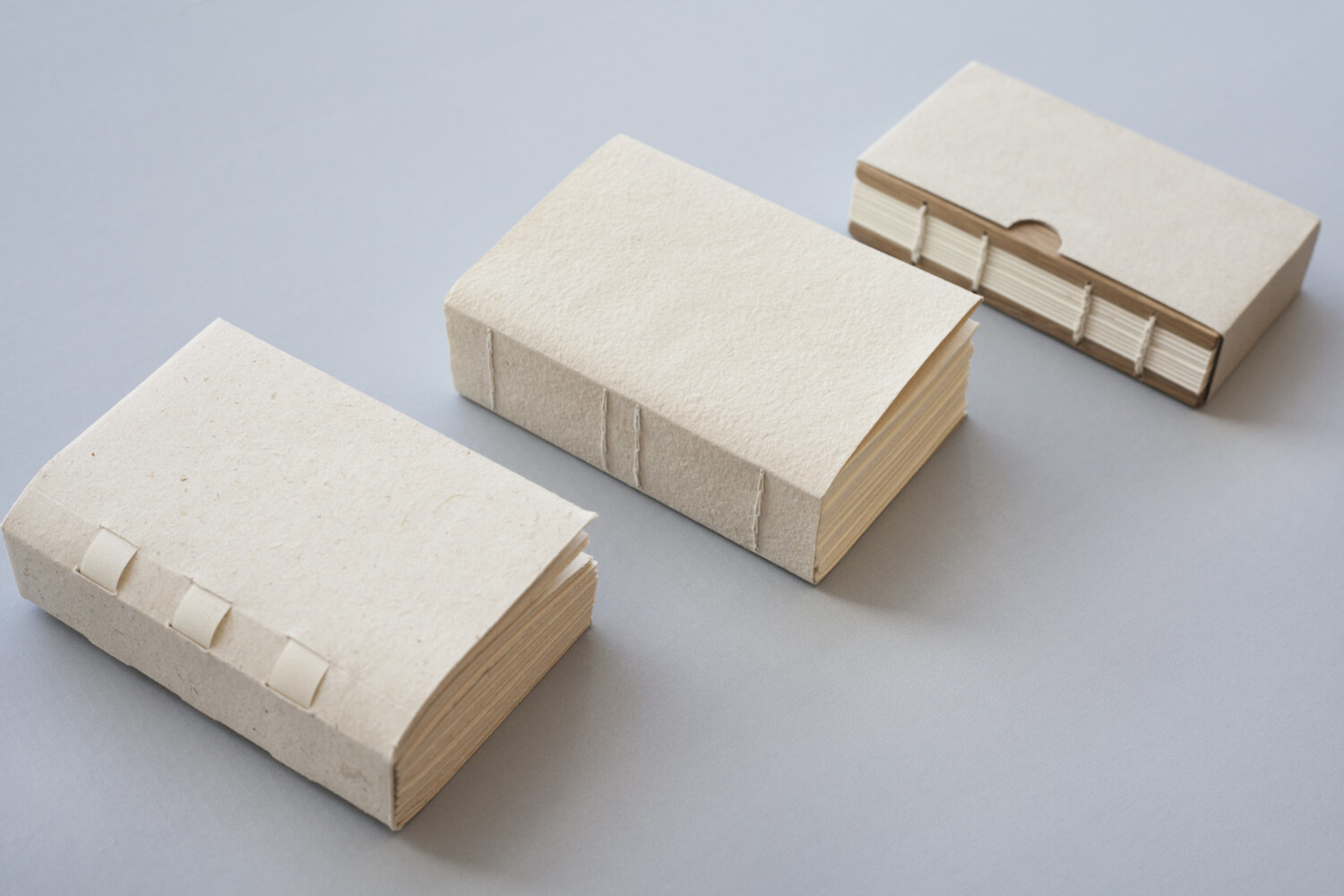
Context
Fresh Press Studio is not the first to propose the use of fibers alternative to bast and wood pulp for paper production. Recent archaeological findings place the invention of paper between 140 and 86 BC in China during the reign of Emperor Wu. (“Early Papermaking”, 2021). Originally, hemp, bamboo, and other plant fibers were the basis for paper before the eventual shift to trees; however, the handmade process remains almost the same today – molds, water, sizing, and pulp.Papermaking came to North America in the 17th century, where predominantly cotton rags and other plant fibers were used for paper. Matthias Koops, whom Dard Hunter praised in his seminal book, was a pioneer in the area:“In the search for new papermaking materials the work of Matthias Koops towers above all of his predecessors, for Koops is responsible for the growth of the paper industry as it is today . . .It was Koops . . . who first made use of various vegetable fibers on a large commercial scale.” (Hunter, 1943, p. 332)
Koops, like Fresh Press, believed in the potential of agricultural fibers for paper and beyond, so he printed a treatise about papermaking on a paper made from straw. (Fig. 8).
Fresh Press has picked up the research, which ended due to wood fiber popularity in the 19th century, to create 21st century sustainable agricultural fiber papers and building materials. As a contemporary practice, hand papermaking is part of the re-crafting movement (as is screen-printing, for example). It’s a return to making by hand (Fig. 9), a rejection of mass production that embraces sustainability as a core value. Re-crafting is a close cousin of the maker's movement where community and network are vital for the artist’s or designer’s success.
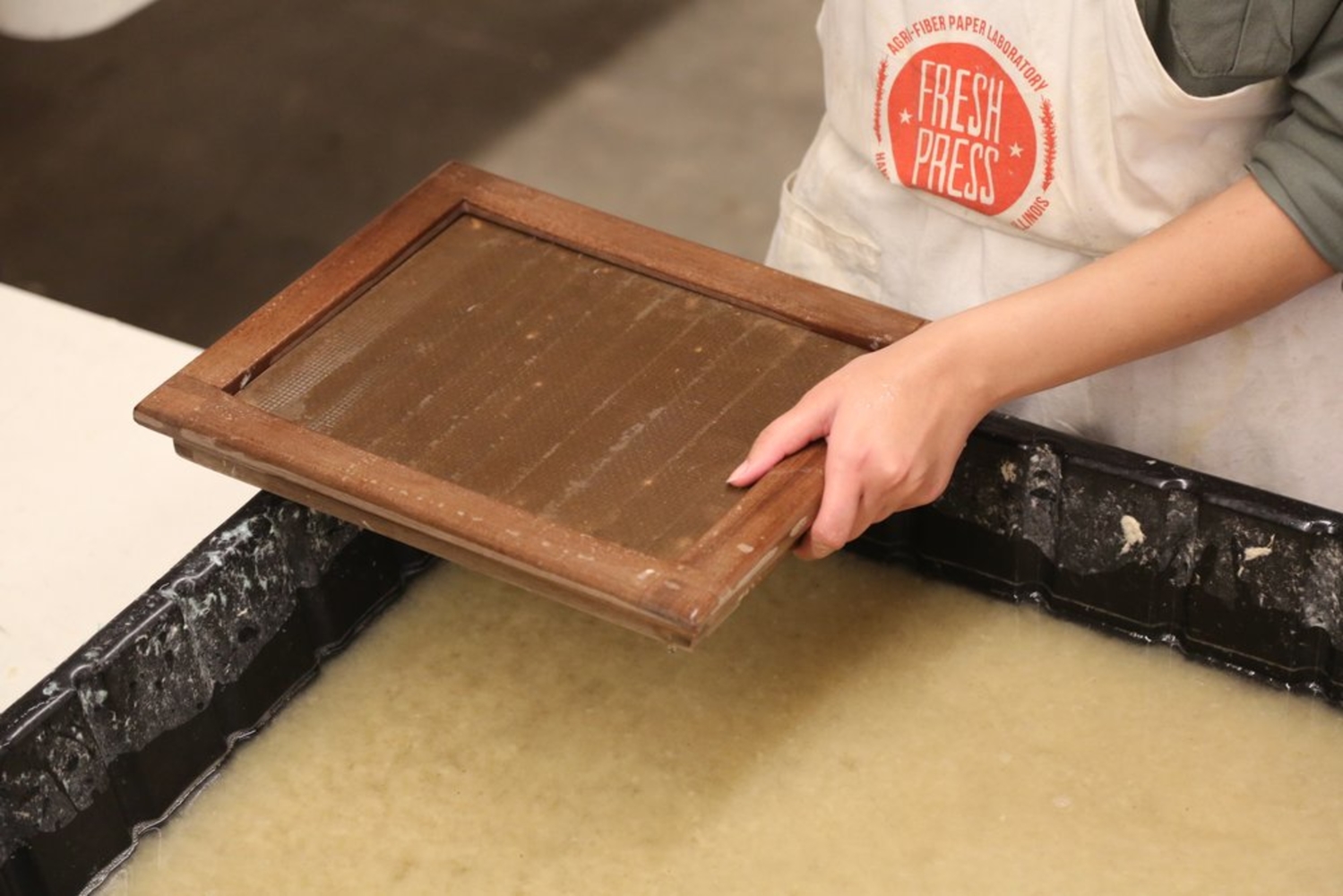
Integration
Fresh Press work is interdisciplinary. With the visibility that comes with funding, good press, successful publications, exhibitions, and awards (2019 GDUSA Graphic Design Award, 2013 AIGA (Re)Design Award), we attract a variety of collaborators interested in the concept of either sustainability or fiber. For instance, both an entomologist, Mike Scharf, and a mechanical engineer, Sameh Tawfick, from the University of Illinois approached us to investigate the concept of “fiber.” The entomologist was interested in small fibers to feed termites to test gut digestive biochemistry changes based on different agricultural diets; the mechanical engineer, who grows carbon nanofibers in a lab, was intrigued by the great strength of some plant fibers and studied them on a microscopic scale as a comparison to his nanofibers.
These collaborations led to others in similar and different disciplines. For example, the data collected with the mechanical engineer helped attract a relationship with the Conservation Lab at the University of Illinois Library to create a sustainable case paper for bookbinding. The papers made for both collaborations were appealing to artists and designers globally who purchased the paper or commissioned us to create a specific size, fiber, and quantity for a project about sustainability. To complete either the research or commissions, we trained and hired both undergraduate and graduate students in the art of papermaking. Their education in this craft helped bring issues of both sustainability and paper into their personal artistic practices. Other University of Illinois faculty noticed this and commissioned Fresh Press to make paper for foundation drawing and printmaking courses, holiday cards, and student recruitment.
Our Main Pseudopods: Research Interests and Methodology
As the Fresh Press ecology is amoebic, it is constantly shifting by semester in focus on a few consistent themes within the lab—research, outreach, education, and entrepreneurship. Our research methodology is one typical of designers and artists. We explore through making. I follow the make, write, reflect method from the book Design Writing Research by Abbot Miller and Ellen Lupton. This style of research has worked well in collaborations within the arts, where scholars use similar or compatible research methods. However, as we work more in the sciences, we have adapted to include more of the scientific method in our research methodology.
There is something to be said about the similarities between making-based approaches and the scientific method. Each requires some systematic way of setting parameters to work, analyze, and try again to achieve success. I do think those similarities in research methods are why Fresh Press has been able to function on equal footing with their scientific colleagues. We can find not only common ground and interest, but also commonalities in our processes.
A successful example of this research blend is a recent partnership with the University of Illinois Library Conservation Unit for a project entitled Prairie Paper. We received a grant of $13,673 from the University Library to develop a paper stock to rival the utility of the Iowa Case Paper for book conservation while maximizing the use of sustainable fibers from the region. Our goals were to show proof of concept working collaboratively across colleges to create a new, locally sourced and produced paper to be used in cultural heritage conservation; to test material and chemical characteristics to determine the best source and production details of a new paper; and to test the resulting materials in a conservation setting to ensure practical use in the field.
In the first three phases of the research, we learned, through tests performed in an engineering lab and from chemist Anneka Vetter, information about the characteristics of our papers such as pH (Fig. 11), fiber length, grammage, thickness, hydrophobicity (Fig. 12), color, speckliness, texture, flexibility, opacity, scorability, foldability (Fig. 13), and burst. This information helped us create four beautiful case papers, one of which may be the final blend of regional agricultural fibers that we push into production. Within this blend of fibers will be an indigenous Illinois prairie grass. Previously, we had used a life cycle analysis software to learn that our prairie grass-based papers have 66% less of a carbon footprint than their tree-fiber counterparts (Fig. 14).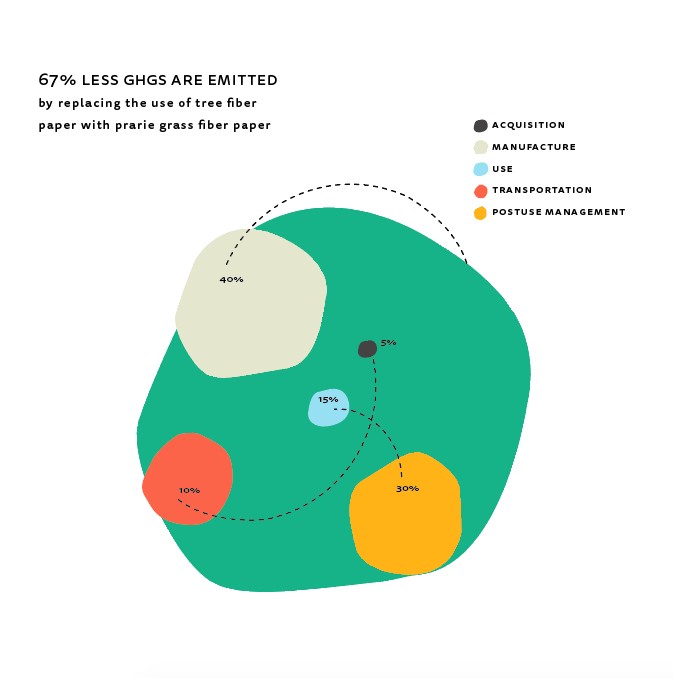
As sustainability is at the root of our project, we want to educate others on our efforts. Beyond the Prairie Paper project, we have data from conducting life-cycle analyses on our other papers we make. We include this data on our website to continually promote our mission to change the paper supply chain from forest to farm, and to attract new collaborators as they can see we are effective in our efforts. Not all our endeavors end in accolades. We wrote a proposal to the University of Illinois to help fund the installation of solar panels on our studio roof; however, since our facility, a pole barn, is considered a temporary structure, there was uncertainty about its long term use and the proposal was denied. We include those failures on our website next to our achievements to attract collaborators who see them as opportunities to help us achieve our environmental goals.
Public Engagement and Education
The public outreach arm of Fresh Press grew from our exposure in the media and our desire to educate our campus and community about sustainability through the lens of paper and agriculture. We opened our doors in 2019 to free and fee-based papermaking workshops (Fig. 15). The most commonly attended workshop is a three-hour Introduction to Papermaking, teaching children to adults the basics of Western papermaking with recycled cotton pulp. We show them the paper beating process before they pull and press sheets and load them into the drybox. We provide food and coffee, and they leave with pre-made sheets and some Fresh Press swag (Fig. 16). Due to the size of the studio and attention to each participant, we limit these workshops to five to six participants; they are always led by a student we trained.
Fresh Press has also traveled to local elementary schools, places of worship, and organizations like the 4-H Club to provide free workshops to children. Beyond the local area, we have also traveled to Iowa State University and the University of Wyoming for workshops and public lectures.
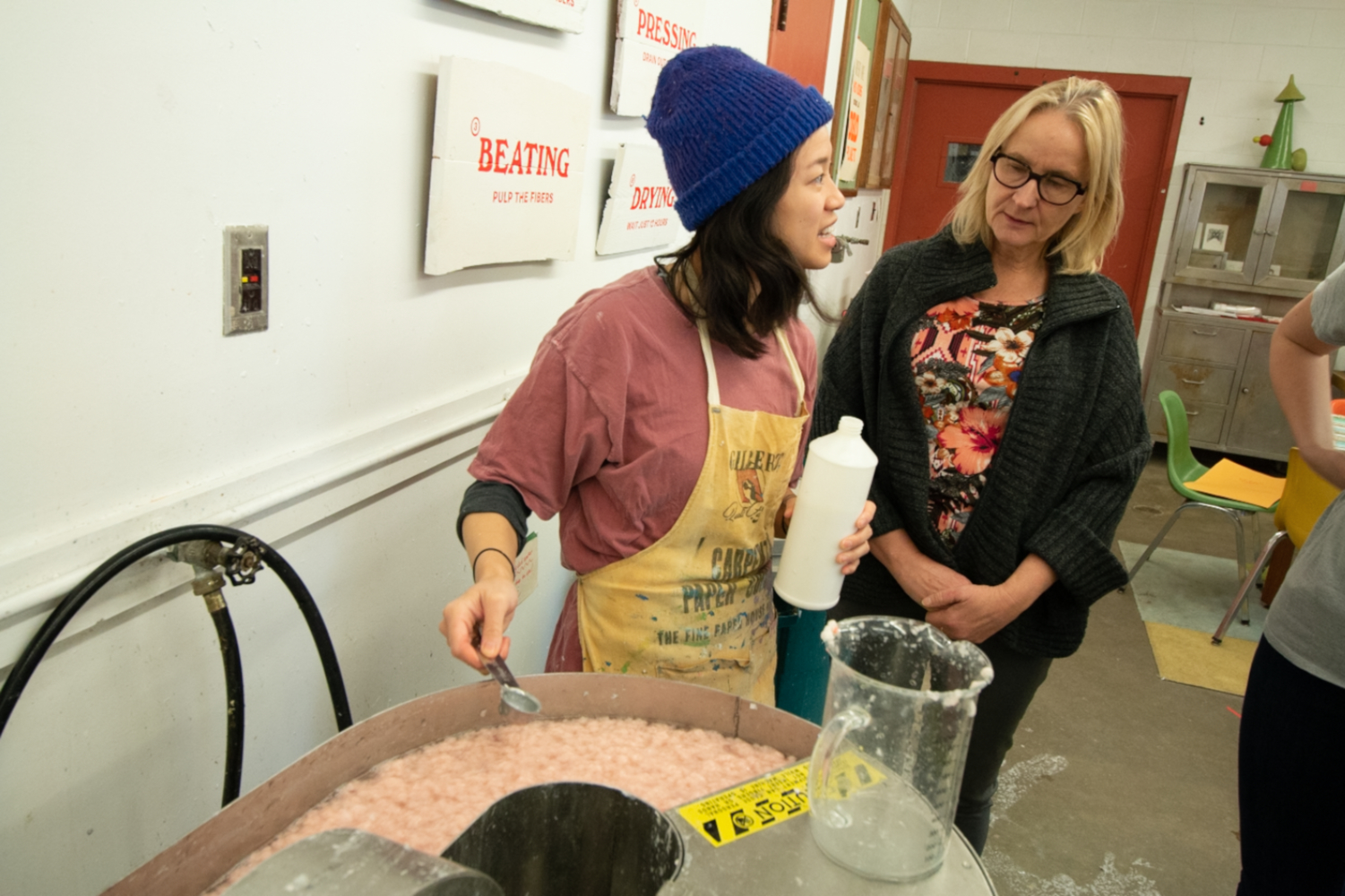
Prior to the community workshops, we trained University of Illinois students whose majors ranged from design to advertising to library science. After they were trained, they were given access to the studio to create their own work, and become more involved in our research and paper commissions. Some of these past students like Megan Diddie, Veronica Pham, and E. Horan returned as artists in residence after graduation. Each was given a workspace for a few days to a year (depending on the proposed project) at Fresh Press to create a body of work using paper or pulp created with our equipment .
Beyond artists with a prior connection to Fresh Press, we developed application processes and policies for external artists in residence. These residencies are structured in two ways. The first is more typical: an artist visits the lab for a period of time, is trained on our equipment, and then has full access to create their work. In the second, a new graduate student makes the case to place their research studio in ours for two to three years. We’ve hosted two external Chicago-based artists in residence and housed four MFA students over the past four years. They have produced work ranging from sculpture (Fig. 17) to installation (Fig. 18, Fig. 19).
These residencies are learned through collaborations Fresh Press has had with other papermakers like Jessica Cochran, Melissa Potter, and Drew Matott from the Peace Paper Project. Each has visited our studio to create works of their own, and spread the story of Fresh Press to their creative networks.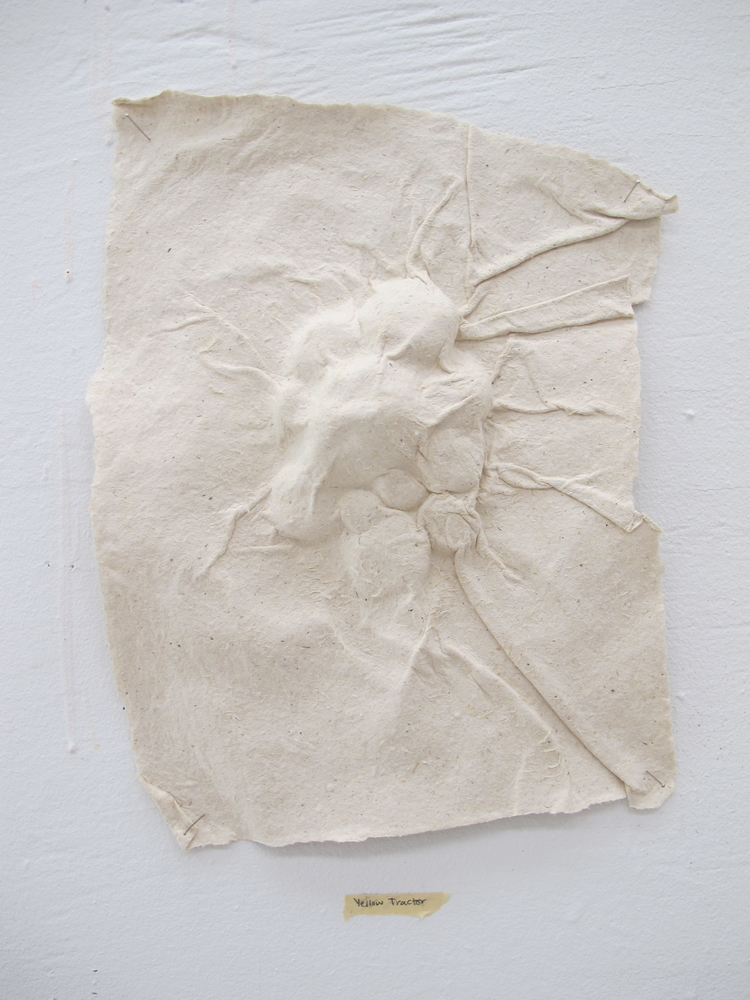
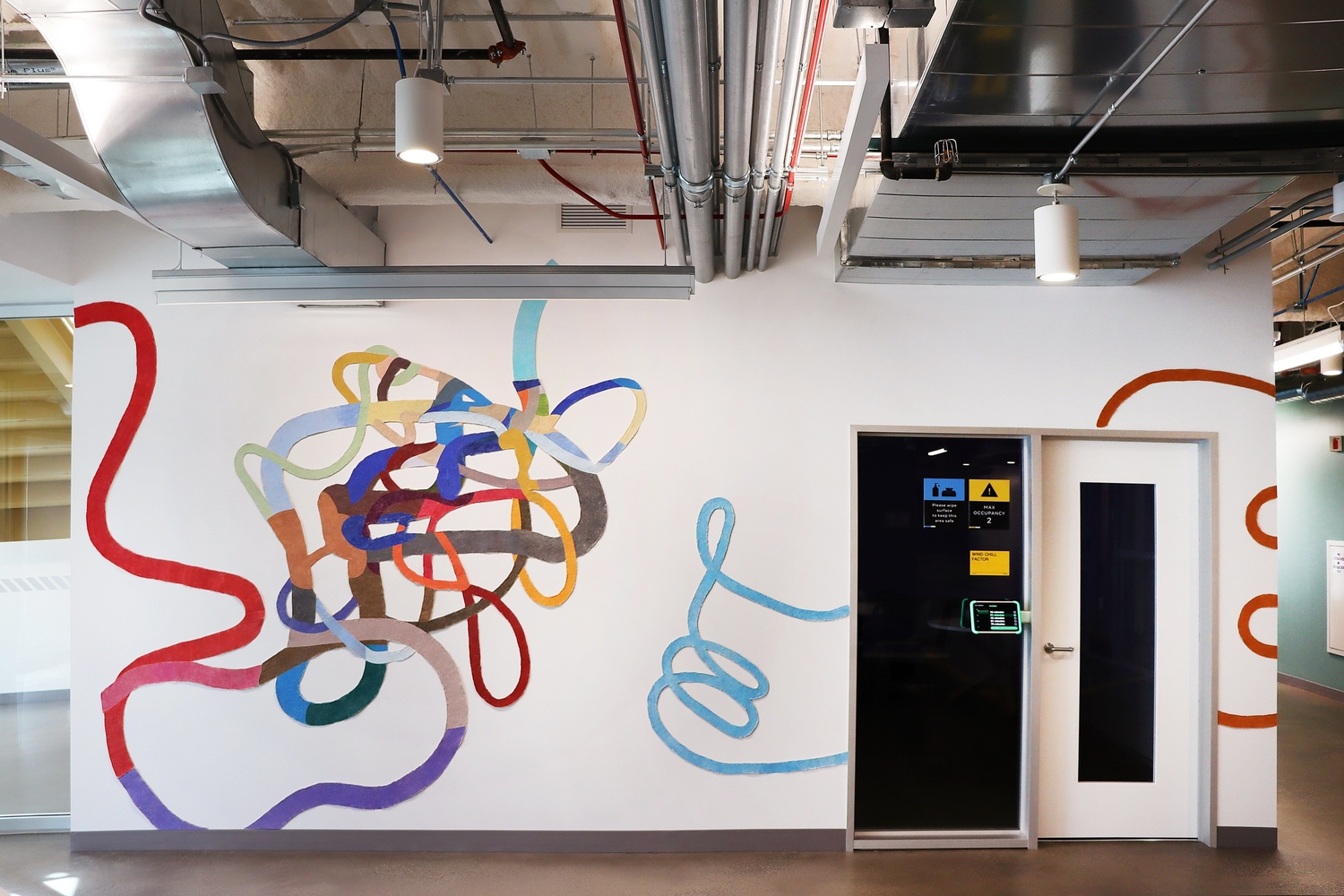
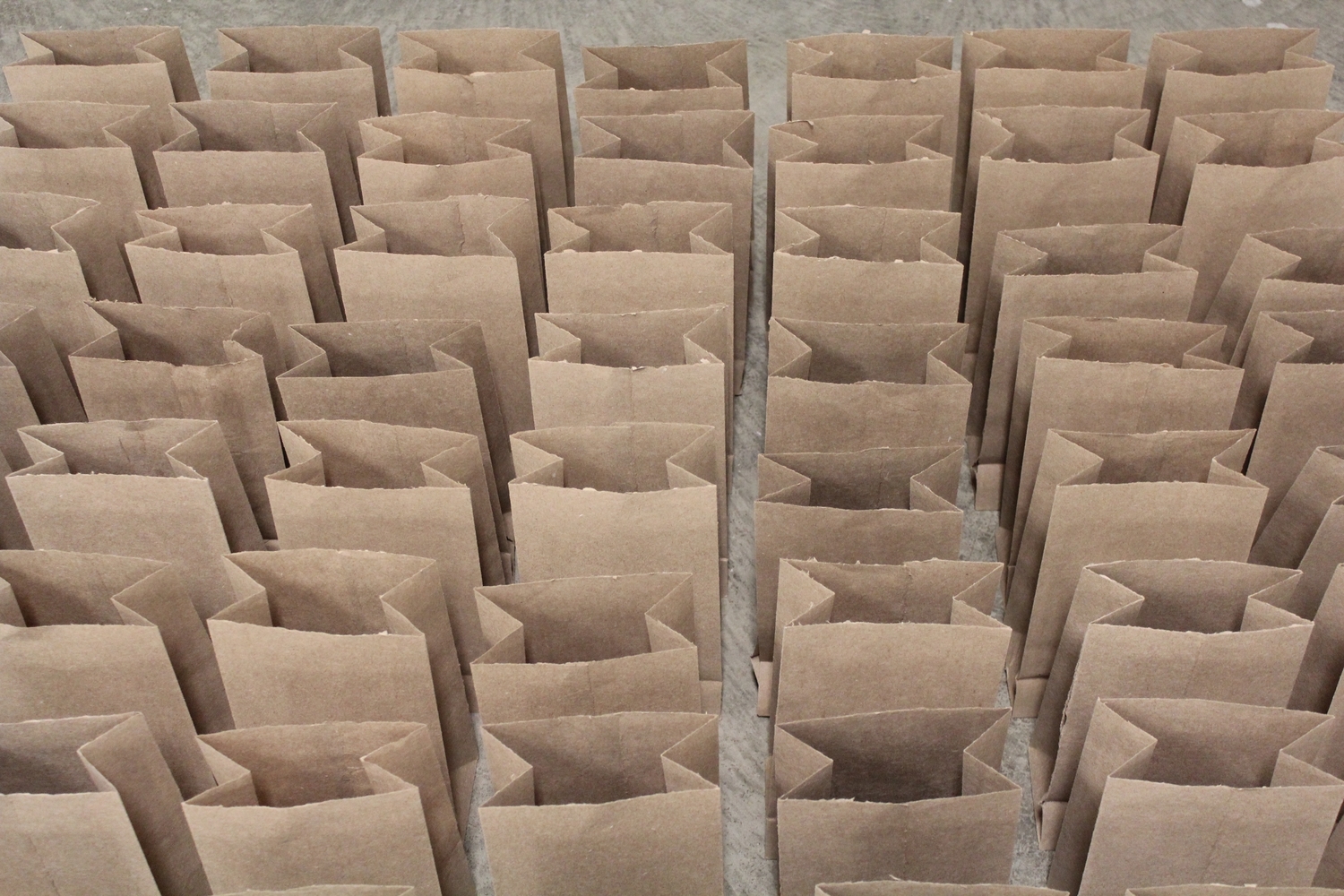
Entrepreneurship
As students became more involved with the studio post-training and workshops, they helped grow our amoebic structure further into the world of commerce. As young artists who want their work to be economically sustainable post-graduation, they need to learn about and become adept in promoting and selling their artistic outputs. In 2016, students helped create and fund the “Fiber CSA (Community Support Agriculture)” project (Fig. 20) where entrepreneurial designers and artists made and sold monthly shares of paper and art prints on paper made from corn, prairie grass, and soy. “Fiber CSA” was the catalyst for invitations to sell our cards (Fig. 21), paper, and prints at regional maker fairs and boutique stores. The press coverage of “Fiber CSA” drummed up interest for new paper commissions, community paper workshops, and artist residency applications. A set of two notepads from the CSA called the “Fiber by Fresh Press Writing Share” is now housed in the Peace Paper Archives at the Robert B. Haas Arts Library at Yale University.
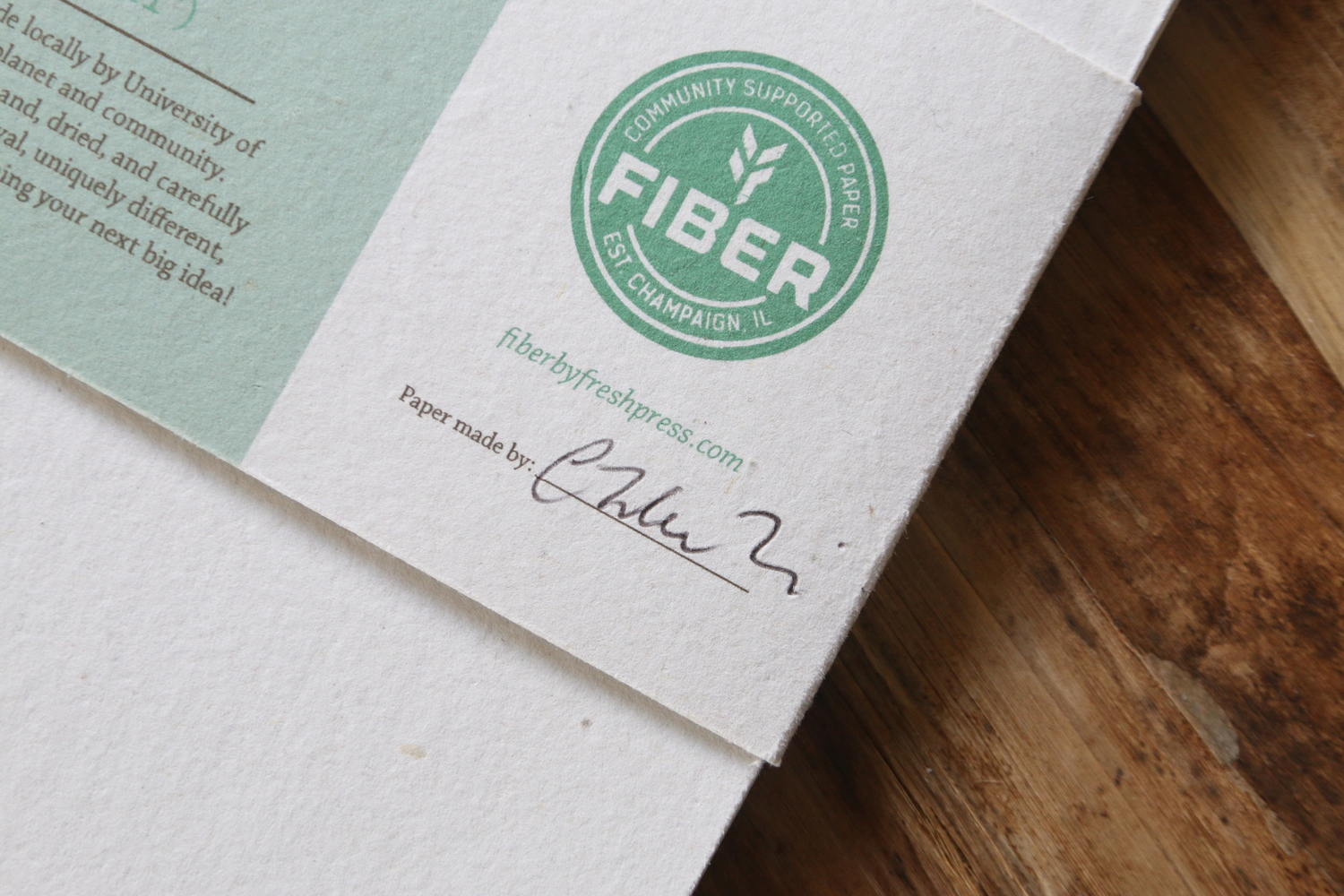
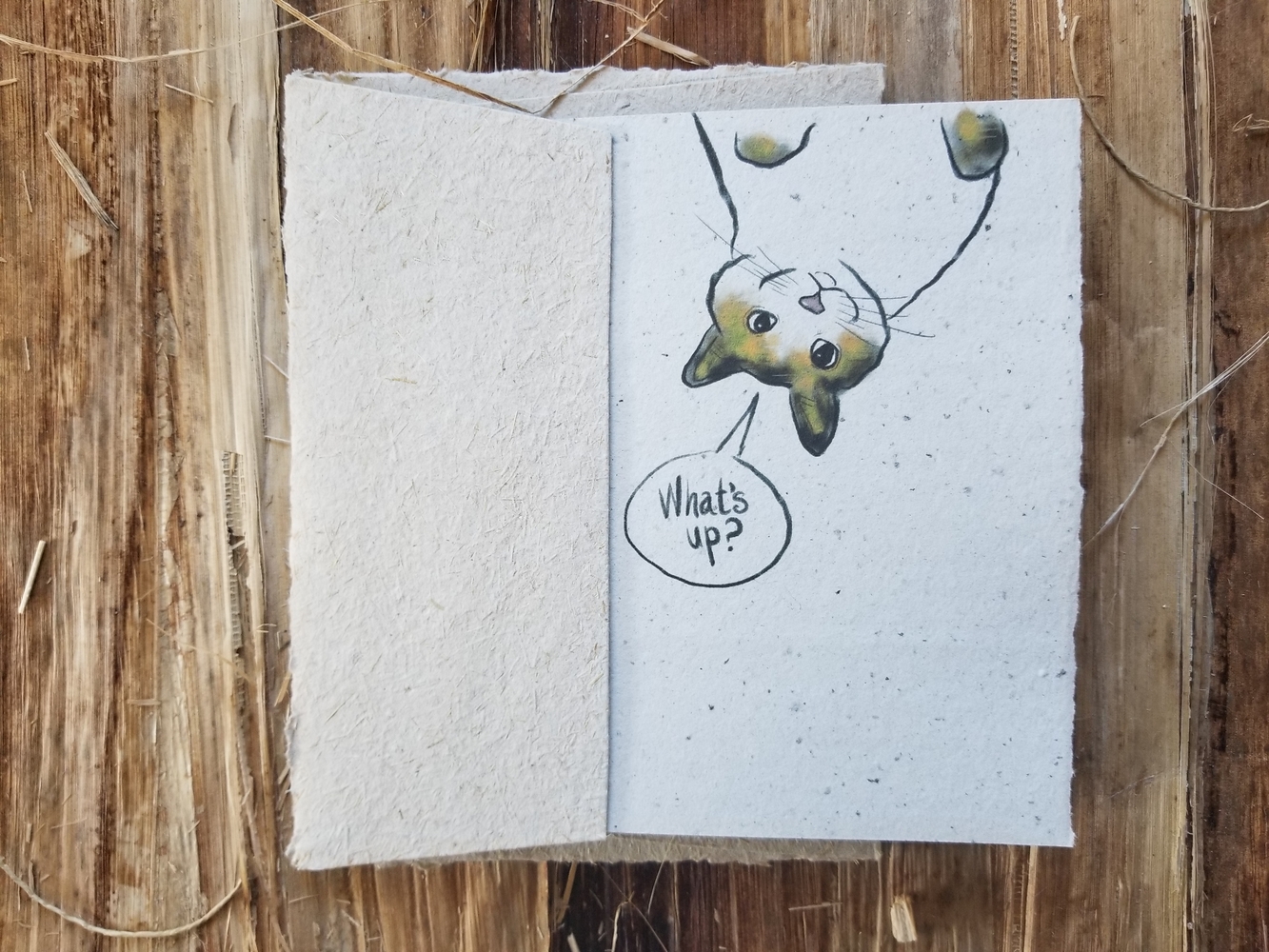
This entrepreneurial shift for Fresh Press was temporary, as the core student leaders graduated and were unable to recruit replacements, but is always an option with new collaborators.
Going Forward
Fresh Press remains steadfast, a research-based lab focused on shifting the paper supply chain from forest to farm. Our interdisciplinary fiber research generates environmental and paper strength data geared towards providing commercial paper companies the knowledge and recipes to shift their fiber away from trees to agricultural fibers. However, as Fresh Press changes form, amoeba-like, new members to our collaborative team consistently help reshape our initiatives and outputs. Currently (2021), a University of Illinois environmental science undergraduate at Fresh Press has quickly morphed our immediate future forecast to collaborate with green businesses she knows in the county. Our initial conversations have evolved toward using a for-profit business to sell paper that uses its packaging to educate about sustainable consumption. We plan to provide paper for sale in their stores and help the business owners promote papermaking workshops on-site to local children. The connections made from these interactions will undoubtedly continue to reshape our vibrant ecologies of research at the lab.
Additional Media
- Conscious Creators, Co. interview with Fresh Press
- News at Illinois interview with Fresh Press
- WCIA3 Story about Fresh Press
- Prairie Paper Advertisement
Bibliography
Braungart, M., McDonough, W. 2002. Cradle to Cradle: Remaking the Way We Make Things. New York, NY: North Point Press.
“Early Papermaking.” Paperdev Gatech Edu. Georgia Institute of Technology. paperdev.gatech.edu/early-papermaking. Accessed 28 Sept. 2021.
Hunter, D. 1943. Papermaking: The History and Technique of an Ancient Craft. New York, NY: Dover Publications.
Koops, M. 1800. Historical Account of the Substances Which Have Been Used to Describe Events and to Convey Ideas from the Earliest Date to the Invention of Paper. London, UK: T. Burton.
Lupton, E., Miller, A. 1999. Design Writing Research. New York, NY: Phaidon Press.